Types of Aluminum Finishes and The Uses of Each
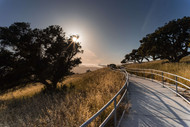
Aluminum is multifunctional, lightweight and relatively low-cost, making it an excellent choice for your next project. However, when it comes to types of aluminum finishes, there are several options you might be curious about.
But what’s an aluminum finish, and why choose one? Aluminum finishes offer:
- Corrosion resistance: While aluminum’s natural oxide film protects it from corrosion, additional protection may be warranted, especially in extreme environments.
- Enhanced appearance: An aluminum finish offers a cosmetic touch, including various colors, textures and sheens.
Today we’ll explore six different types of aluminum finishes to help you decide which one is right for your use case.
1. Surface/Mechanical Finishes
Treating aluminum with mechanical finishing techniques can improve its surface or functionality or prepare it for other finishes. Whether you wish to buff the extrusion to a sheen, add texture or something in between, there are several ways to go about it.
Aluminum and aluminum alloys can be:
- Milled: The basic finish of most aluminum extrusions
- Blasted: A high-pressure treatment that cleans and finishes an extrusion
- Brushed: Typically used before anodizing to create a uniform surface grain
- Grinded: To create a smooth surface
- Polished and buffed: To remove imperfections and create a mirror finish
2. Pretreatment/Chemical Finish
Like mechanical or surface finishes, pretreatment or chemical finishings prepare extrusions for other finishes. The aluminum is cleaned or etched with acidic or alkaline materials, then dipped into a pretreatment coating. This coating enhances powder coat or wet coat adhesion and provides resistance to corrosion.
Chemical Finishes Include:
- Etching: For a matte or satin finish
- Bright-dipping: For a high quality, shiny finish
3. Anodized Aluminum
Anodizing is an electrochemical process that supplements the protection of aluminum’s natural oxide layer. During anodizing, aluminum is immersed in a chemical bath containing acid-based electrolytes. Then, an electrical current is passed through the liquid, creating a durable aluminum oxide layer that preserves the aluminum’s texture and luster.
Anodizing aluminum enables it to accept vibrant color treatments. Any aluminum alloy can be anodized.
Use Cases for Anodized Aluminum
Anodized aluminum has hundreds of use cases. Common applications include:
- Appliances and furniture
- Residential and commercial building products
- Interior decor
- Food preparation equipment
- Sporting goods
- Motor vehicle and aerospace components
- Art and jewelry
4. Powder Coated Aluminum
Powder coating can be similar in appearance to wet coated aluminum but is much more durable than paint. The process of powder coating aluminum involves melting statically charged powder onto aluminum in a curing oven, which produces a glossy, matte or textured coating depending on the desired finish.
Powder coating does not contain VOCs (volatile organic compounds), gases emitted into the air from processes or products. This makes powder coated aluminum exempt from certain environmental regulations that forbid VOCs.
Use Cases for Powder Coated Aluminum
You might think of powder-coated aluminum as the best of both worlds: lightweight and long-lasting.
In addition, it can withstand harsh weather without corroding, making it an excellent choice for:
- Patio furniture
- Doorknobs
- Railings
5. Wet Coated (Liquid Paint Coated) Aluminum
To wet coat or liquid coat aluminum, pressurized sprays or pumps are used to apply paint to the surface evenly. The painted extrusion is then baked or cured to set it.
Unlike powder coating, liquid coatings do contain VOCs; however, they are shed during the baking process. When VOCs are eliminated, the solids form a uniform film thickness on the extrusion.
Liquid paint coated aluminum is often smoother than powder coated aluminum, which can sometimes have a bumpy or “orange peel” texture. Liquid paints for aluminum are available in various colors and formulas, including acrylics, polyesters and fluoropolymers.
Use Cases for Wet Coated Aluminum
Painting over the surface of aluminum changes its appearance and helps protect it against corrosion. Common applications include:
- Playground equipment
- Railings
- Window frames
- Flagpoles
6. Plated Aluminum
Plating coats aluminum with a thin layer of another metal, like chrome, gold, silver or brass plate. This is done through electroplating (using electric current) and electroless plating (using autocatalytic chemicals).
Use Cases for Plated Aluminum
- Automobiles
- Aircrafts
- Motorcycles
Complete Your Next Project With Orange Aluminum
Choosing the right aluminum finish will ensure that your project ends up with the appearance and durability you desire.
We hope this article has been helpful to you. However, if you have additional questions about aluminum finishes or are looking to choose an aluminum supplier, our team is glad to help!
Orange Aluminum works directly with local mills to provide the most competitive pricing to our clients. With primary locations in Orange County and Los Angeles, we serve customers from any location in the United States.
Our strength is our customer service, and aluminum is our specialty! Want a quote for your next project? Contact us today -- we’re happy to help!