Mill Finish Aluminum vs. Clear Anodized Aluminum
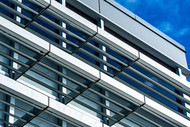
Depending on your circumstances, choosing between aluminum and other metals tends to be a straightforward decision. Aluminum is durable, strong (especially aluminum alloys), flexible, corrosion-resistant and completely recyclable.
It’s also the most abundant metal on our planet—despite once holding greater value than gold. However, choosing which aluminum finish best suits your needs is a bit more nuanced. To that end, is a mill finish aluminum or anodized aluminum right for your needs?
Let’s extend the discussion a bit further to break down the differences between both.
Head-to-Head: The Quick Answer
Mill finish aluminum is your best economical choice for non-corrosive environments and if outward appearance isn’t a priority. In comparison, clear anodized aluminum — or other colors — provides better:
- Aesthetics
- Surface durability
- Resistance against corrosion (e.g., salt, water and UV light)
As a result, anodized aluminum typically scales in value, making it pricier.
What is Mill Finish Aluminum?
Mill finish aluminum is the technical term for “raw” or unfinished aluminum material that does not undergo any treatment process. For extruded aluminum, that means the starting billets are heated and hydraulically pressed through a steel die to take their final shape before they’re cut to length and shipped.It comes straight from the mill floor, as is.
The Natural Oxidation of Aluminum
While “raw” aluminum doesn’t rust, per se, it is still quite reactive and corrodes when exposed to wet, salty and other corrosive environments — such as those outside an approximate pH range of 4 to 9.
Yet, aluminum’s reactiveness is actually rather short-lived.
The layer of aluminum oxide (i.e., Al2O3) that forms on the surface and chemically bonds with the metal makes it generally passive. This significantly protects aluminum materials against further corrosion.
You can think of this process as oxygen slowly absorbing into the aluminum. Once the surface has sufficiently oxidized, it creates a barrier that prevents further absorption. Corrosive exposure, however, allows oxygen to penetrate the aluminum further, which causes more substantial degradation over time.
Aluminum oxide can be seen — or felt — as a white powdery substance, but the oxidation layer is chemically bonded to the metal. The naturally occurring layer for mill finish aluminum products is roughly 2-3 nanometers (nm) thick.
Mill Finish Aluminum: Pros
The most significant advantage mill finish aluminum offers is that it’s the most economical choice. Since no finishing process is applied, and the protective oxidation naturally occurs regardless, it’s inherently less expensive to produce.
Mill Finish Aluminum: Cons
Aluminum products perform well and are highly reliable, but — in comparison with finished aluminum — the cons revolve around the need for further treatment to provide even better protection and performance.
Treatments such as anodizing aluminum will hold up better against everything from surface nicks and scratches to corrosive environment exposure. Even the extrusion process of pushing the material through the die can leave behind (nonstructural) marks and discoloration.
The difference in durability is due to the oxidation layer’s thickness. It’s why mill finish aluminum tends to be favored primarily for dry locations or uses where it won’t be visible.
What is Clear Anodized Aluminum?
The process of anodizing aluminum involves oxidizing the aluminum through a controlled process that creates a thick, protective layer on the metal. It’s one of the most common aluminum finishes.
Anodizing also provides better coloration. “Clear anodized aluminum” merely refers to anodized but uncolored products, which results in a silvery finish that maintains an attractive sheen.
What is Anodization?
Anodization is an electrochemical process that “forces” increased oxidation in a controlled manner. The layer simultaneously “expands” into and grows out of the aluminum material.
In this process, aluminum products are dunked into a sulfuric acid bath (i.e., H2SO4) and exposed to an electric charge. This creates a thick anodic oxide layer called anodic aluminum oxide (AAO). This hard, durable outer layer protects the underlying aluminum, improving its wear resistance.
Why Anodize Aluminum?
The AAO layer created via anodization is roughly 500 -150,000 nm thick, and manufacturers retain extremely dialed-in control over achieving the desired thickness for specialized purposes (e.g., construction and architecture). The layer’s thickness can be affected by variables such as:
- Time in the acid bath
- Temperature of the acid bath
- Strength of the electrical current
With that much control, manufacturers can create a corrosion-inhibiting AAO layer between 250-50,000 times thicker than would naturally occur.
Aside from providing greater protection, anodization also removes aesthetic imperfections, such as marks and patterns caused by the extrusion process or rough handling.
Colorization vs. Clear Anodized Finish
AAO is porous and resembles a fairly uniform, honeycomb-like pattern. By filling the pores with pigment and then sealing them, you can also apply colors and tints directly to the metal. Since the AAO layer is a chemical bond, the color won’t chip or scratch like paint eventually will.
We provide six different color options for anodized aluminum:
- Clear/silver
- Black
- Dark bronze
- Medium bronze
- Light bronze
- Gold
A clear anodized finish is the result if no color pigments are used before applying the sealant. In the same way wood finishes protect and beautify the wood, clear anodized aluminum protects and enhances aluminum’s natural, silvery appearance.
Clear Anodized Aluminum Pros and Cons
If the aluminum will remain exposed to elements, anodized material will provide optimal performance and durability. Particularly in humid and coastal environments, the thicker AAO layer better prevents corrosion.
If aesthetics matter, anodized aluminum will not only maintain a beautiful, polished appearance without die marks, but the material also remains scratch and damage resistant throughout its use and handling.
The only real disadvantage of using anodized aluminum is that the finishing process adds to the final cost of the product. If your project requires a significant amount of material, this could certainly affect the overall budget.
Complete Your Next Project with Orange Aluminum
If you need to maximize the durability, corrosion resistance and beautification of your extruded materials, you’ll want to use clear anodized aluminum. If environmental conditions won’t impact durability — and no one will be fussy about appearances — mill finish will still do the job extremely well.
No matter your finish choice, Orange Aluminum is your top provider. Since 2007, our friendly and helpful team has grown into one of the nation’s top providers of extruded aluminum trim, shapes and bars.
With 1000+ extrusion profiles, 1,000,000+ pounds of inventory, and plenty of customization options, we’ll ensure our aluminum extrusion products meet your needs. And if you want an item in another finish, we can do that too.
Connect with us today to start your custom aluminum order!