Annealing Aluminum Explained: What It Is and How It Works
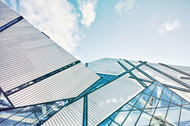
Like many metals, aluminum is subject to work hardening—also known as strain hardening. This means it becomes more challenging to work with the more it is deformed and shaped.
Annealing is a heat-treating process relied on to “reset” work-hardened aluminum. It’s commonly used when the metal must be shaped into more complex forms through repeated plastic deformation.
Here’s our primer on the what, why and when of annealing aluminum.
What Is Annealing
Annealing is a heat-treatment process used by metalworkers on their material to:
- Soften
- Reduce stress
- Improve workability
Aluminum may be fully or partially anneal aluminum, depending on the required mechanical properties of the finished product.
Metals like aluminum are annealed because they’re more likely to experience strain hardening. As a soft metal to begin with, aluminum often undergoes plastic deformation when being shaped—or permanent shape changes resulting from applying tensile, compressive, bending or torsion stress.
One such deformation process is extrusion, as the metal is forced through a steel die orifice, much like when kids press “Play-Doh” through differently shaped cut-outs or pasta dough is made into spaghetti.
How Annealing Works on Aluminum Grain Structures
Annealing allows aluminum to be shaped beyond its usual capacity at a molecular level.
The microscopic grain structures of aluminum and other work-hardening metals are deformed during shaping processes, and—as they are continually worked—they become increasingly resistant to deforming or stretching further.
At a certain point, these grain structures can’t experience any more stress without the metal breaking, cracking or eventually warping (under excessive internal stress).
Before that happens, aluminum is annealed—or heat-treated for a set length of time, often in a specialized furnace or via torch flame (e.g., acetylene). Annealing resets those aluminum grain structures, allowing the material to undergo further shaping with ease.
To anneal aluminum, the metal must be heated between 570°F and 770°F, with specific temperatures and durations determined according to each aluminum alloy’s own characteristics and the amount of material. Crucially, the cool-down period following the annealing process can also affect material and physical properties.
So, annealing is generally performed in highly controlled environments, with specialized equipment and cooling methods. Although it's much less precise, at-home or on-site annealing can still be performed with a torch.
What Purpose Does Annealing Aluminum Serve?
Sometimes, strain hardening is a benefit, as it makes aluminum more difficult to deform further. For a finished piece or part, this might be ideal.
However, when aluminum must be significantly deformed or worked into complex shapes, strain hardening:
- Prevents successful shaping
- Increases the metal’s internal stress and makes warping more likely
- Can result in physical marks, like whitening, or structural damage, like cracks
- Leaves products more susceptible to breaking if they suffer an impact while in-use
- Results in greater wear on tools and equipment, like those for shaping, cutting and grinding
Intricately shaped automotive or aerospace parts are examples where aluminum may need to be annealed multiple times before the final shape is achieved. Still, even simple shapes can benefit from the annealing process.
Pragmatic Examples of the Benefits of Annealing Aluminum
Consider aluminum tubing, which is used for all types of purposes, especially the metal frames of shelving or outdoor furniture. When the aluminum is extruded into lengths of tubing, it will undergo some strain hardening naturally.
Bending the tubing into its finished shape will harden the aluminum even more. This means that more impact force or weight will be required to deform the metal any further, but there’s also less capacity for it to deform before a complete break occurs.
If someone impacts aluminum shelving with a forklift or places too much weight on top, the metal will break more easily if sufficient force is suddenly applied to strain-hardened materials.
Learn more about the types of aluminum finishes and their uses.
Some aluminum tubing is also used for various fluids, which requires some amount of ductility (i.e., ability to deform). If the tubing containing your car's brake or transmission fluid were to impact something you run over or be hit by small rocks and debris being knocked all about, strain-hardened lengths would be more likely to break than deform. Deformed tubing can still perform its purpose, if less optimally, but breaks and cracks will result in fluid leaks.
For structural or essential aluminum parts, they must withstand critical failure if they can still function while slightly deformed.
Terms and Definitions Important for Understanding Annealed Aluminum
When considering different annealed aluminum products—or annealing aluminum material yourself—you’ll need to be familiar with certain terms and their definitions:
- Work hardening (or strain hardening) – The characteristic in some metals, where they become increasingly resistant to further deformation the more they’re already deformed
- Precipitation hardening – A method for strengthening metal by applying high temperatures and adding impurities that prevent grain structure deformation; it’s also known as “natural aging” when performed with lower temperature increases over a longer period
- Plastic deformation – The application—controlled or not—of significant enough tensile, compressive, bending or torsion stress that a material’s physical shape is altered
- Heat treatment – Controlled applications of high temperatures used to alter a material’s characteristics
- Heat-treated aluminum alloys – These alloys become strengthened or hardened when high temperatures are applied to the metal; as a result, they can only undergo limited instances of annealing and require highly controlled cooling and quenching
- Non-heat-treated aluminum alloys – These alloys anneal, or become softer, whenever high temperatures are applied to the metal, making the process continually repeatable
- Cold working – This refers to metalworking and shaping processes that do not require heat to perform, such as bending aluminum tubing
- Ductility – The material properties of a given metal that enable it to permanently deform under various stresses; more ductile metals are described as being “softer”
Annealing Aluminum Alloys
Depending on whether the aluminum alloy being worked on is heat treatable or not, the annealing process will have varying effectiveness, increased considerations, and limited repeatability.
The cooling process also varies significantly, with more steps for heat-treated aluminum.
Welding is one application where deciding between heat-treated and non-heat-treated alloys is crucial. The former will likely lose mechanical strength, and many welding filler alloys that would be used are not suited for post-weld heat treatments unless they've been specialty-developed for it.
Heat-Treated Aluminum Alloys
Heat-treated aluminum alloys contain other elements that become more soluble—or “blend” better and more uniformly—at higher temperatures. Higher temperatures are necessary for heat-treating aluminum than for annealing it. Still, this results in the alloy hardening, at least partially, and decreases the effectiveness and repeatability of annealing.
Heat-treated aluminum alloys include:
- 2xxx series – Includes copper alloys
- 6xxx series – Includes magnesium and silicon (magnesium silicide) alloys, and this series is the only one comprising exclusively “wrought” alloys
- 7xxx series – Includes zinc alloys
Non-Heat-Treated Aluminum Alloys
Non-heat-treated aluminum alloys are primarily strengthened via strain hardening and softened via annealing.
- 1xxx series – Includes “pure” aluminum
- 3xxx series – Includes manganese alloys
- 4xxx series – Includes silicon alloys
- 5xxx series – Includes magnesium alloys
To Anneal or Not To Anneal? Orange Aluminum Can Help You Find the Answer
Depending on how much you need to work or deform aluminum into its final shape, or whether strain hardening may be less beneficial to your use case, annealing aluminum matters.
Regardless of which aluminum alloy you need, heat-treatable or not-heat-treatable, Orange Aluminum has you covered. We’re a leading supplier of extruded aluminum products, offering over 1000 SKUs. And, our Orange County location allows us to easily overcome shipping and logistics hurdles for deliveries around the country.
Reach out today to find out how we can source the aluminum for your next project.